Technical specifications
Model | COS hydrolysis catalyst |
Color | White |
Shape | Sphere |
Normal size | 3~5mm |
Density | 0.8-1.0 kg/L |
Crushing strength | ≥50 N/cm |
Loss on Attrition | max3% |
COS conversion | min95% |
Pressure | ambient to 5.0 Mpa |
Temperature | 100-40℃ |
LHSV | 3-5 h-1 |
L/D of reactor | min3 |
Sulfur mainly COS | max10ppm |
Water in feed | max1500ppm |
Feature and Typical Application | hydrolysis catalyst is mainly used to promote hydrolysis reaction between carbonyl sulfide and water. It can be used in different combinations with zinc oxide , iron oxide and activated carbon adsorbents according to different application cases to attain deep desulfurization. The main reaction involved is: COS+H2O=H2S+CO2 The catalyst can hydrolyze organic sulfur and adsorb various sulfur compounds. Total sulfur in liquid propylene treated by T-907 and Tc-22 is less than 0.1 ppm. Service life of the catalyst is about one year. |
Loading | (1). Clean the reactor of any debris. (2). Screen out any dust in the catalyst. (3). Install two layers of stainless wire net with smaller mesh size than the catalyst on grid of the reactor. Then install 100mm depth of φ20-30mm inert balls. The catalyst is separated from inert balls by a stainless wire net of smaller mesh size than the catalyst. (4). Load the catalyst evenly from a height of less than 1 m into the reactor using special tools. Make sure that the catalyst is loaded uniformly. If inner-reactor is needed, the operator should step upon wooden plate laid upon top of the catalyst. (5).Install a layer of stainless wire net with smaller mesh size than the catalyst and a 100 mm depth of φ2030mm inert balls or rings to prevent stripping by gas stream and ensure uniform distribution of the gas flow. |
Start-up and shutdown | (1) Close all inlet and outlet valves. Then open feed inlet valve and raise pressure at 0.5MPa/10 min. (2) Slowly open the outlet valve after reactor pressure reaches feed pressure. Run at one-fourth load for 4h . Analyze outlet sulfur and ensure outlet sulfur concentration of less than 0.1 ppm. (3) When outlet sulfur concentration is up to the controlled value, gradually advance to half load and then to full load in several hours. (4) Close inlet valve first and then close outlet valve to disconnect the reactor from system before shutdown. (5) Avoid wide scope fluctuation of pressure and load during operation which may impair the catalyst. (6) Gradual increasing temperature within operating condition range is helpful to enhancing conversion over the catalyst (7) The reactor should be fit up with vent pipeline to avoid contamination to downstream system by desorbed sulfur compounds during shutdown and lowering pressure. |
Products
Molecular Sieve
- 3A Molecular Sieve
- 4A Molecular Sieve
- 5A Molecular Sieve
- 13X Molecular Sieve
- 13X APG Molecular Sieve
- XH-7 Molecular Sieve
- XH-9 Molecular Sieve
- Insulating Glass Molecular Sieve
- Activated Molecular Sieve
- Carbon Molecular Sieve
- ZSM-5 Series Shape-selective Zeolites
- NaY Absorbent
- 4A Molecular Sieve
- 5A Molecular Sieve
- 13X Molecular Sieve
- 13X APG Molecular Sieve
- XH-7 Molecular Sieve
- XH-9 Molecular Sieve
- Insulating Glass Molecular Sieve
- Activated Molecular Sieve
- Carbon Molecular Sieve
- ZSM-5 Series Shape-selective Zeolites
- NaY Absorbent
Activated Alumina
Catalyst
Silica Gel
Activated Carbon
Ceramic Ball
Random Packing
- Ceramic Berl Saddle
- Ceramic Cross Partition Ring
- Ceramic Cascade Mini Ring
- Ceramic Super Saddles
- Ceramic Pall Ring
- Ceramic Raschig Ring
- Ceramic Baffle Ring
- Ceramic 3Y Ring
- Ceramic Wheel Ring
- Ceramic Intalox Saddles
- Metal Cascade Mini Ring
- Metal Raschig Ring
- Metal Super Raschig Ring
- Metal Inner Arc Ring
- Metal Conjugate Ring
- Metal Super Mini Ring
- Metal Pall Ring
- Metal Super Saddles
- Metal Intalox Saddles
- Plastic Sun Protection Hollow Ball for Reservoirs
- Plastic Snow Flake
- Plastic Liquid Surface Covering Ball
- Q-Pack
- Plastic Conjugate Ring
- Plastic Tri-Pack
- Plastic Heilex Ring
- Plastic Teller Rosette Ring
- Plastic Hollow Floatation Ball
- Plastic Polyhedral Hollow Ball
- Plastic Cascade Mini Ring
- Plastic Super Saddles
- Plastic Intalox Saddles
- Plastic Pall Ring
- Plastic Raschig Ring
- Pentagon Ring
- Plastic VSP
- Plastic Hiflow Ring
- Plastic Angular Ring
- Ceramic Cross Partition Ring
- Ceramic Cascade Mini Ring
- Ceramic Super Saddles
- Ceramic Pall Ring
- Ceramic Raschig Ring
- Ceramic Baffle Ring
- Ceramic 3Y Ring
- Ceramic Wheel Ring
- Ceramic Intalox Saddles
- Metal Cascade Mini Ring
- Metal Raschig Ring
- Metal Super Raschig Ring
- Metal Inner Arc Ring
- Metal Conjugate Ring
- Metal Super Mini Ring
- Metal Pall Ring
- Metal Super Saddles
- Metal Intalox Saddles
- Plastic Sun Protection Hollow Ball for Reservoirs
- Plastic Snow Flake
- Plastic Liquid Surface Covering Ball
- Q-Pack
- Plastic Conjugate Ring
- Plastic Tri-Pack
- Plastic Heilex Ring
- Plastic Teller Rosette Ring
- Plastic Hollow Floatation Ball
- Plastic Polyhedral Hollow Ball
- Plastic Cascade Mini Ring
- Plastic Super Saddles
- Plastic Intalox Saddles
- Plastic Pall Ring
- Plastic Raschig Ring
- Pentagon Ring
- Plastic VSP
- Plastic Hiflow Ring
- Plastic Angular Ring
Structured Packing
Molecular sieves for medical oxygenators
A measure to prevent infection
Ceramic grate sulfur noodles
Rashig's crimped rings
Prismatic springs
Kaldens
Products
We are up to date with technical innovations and implement them as part of our offer.
%
Satisfaction
Our products are of the highest possible quality. When you buy from us, you buy safely.
Years of experience
We know everything about our products. Practical knowledge acquired through years of presence in the industry.
Countries
Our brand has visited countries all over the world. We deliver products, among others to Germany, Sweden and the United States.
HurtGral - Your supplier of molecular sieves.
Contact
If you want to discuss your order, ask about products or discuss product specifications, please contact us.
Call +48 792 020 580 or use the contact form.
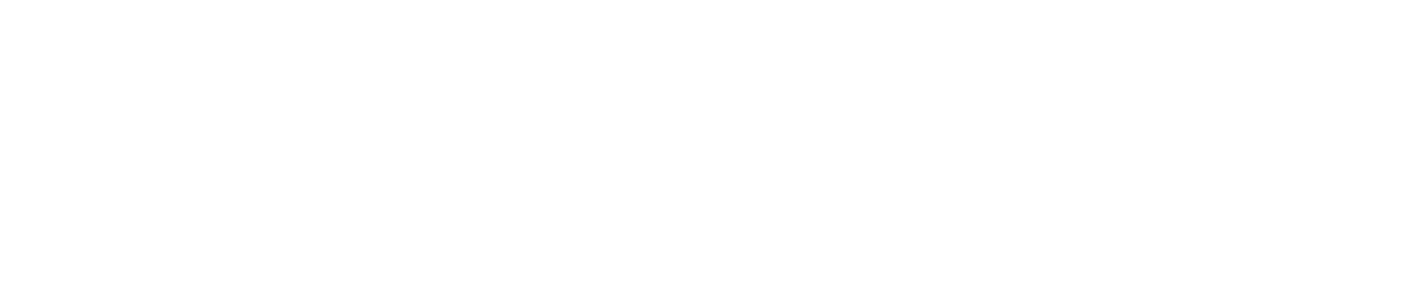
HurtGral - Your supplier of molecular sieves.
Ceramic packing, yeast, enzymes, additives for the food industry.
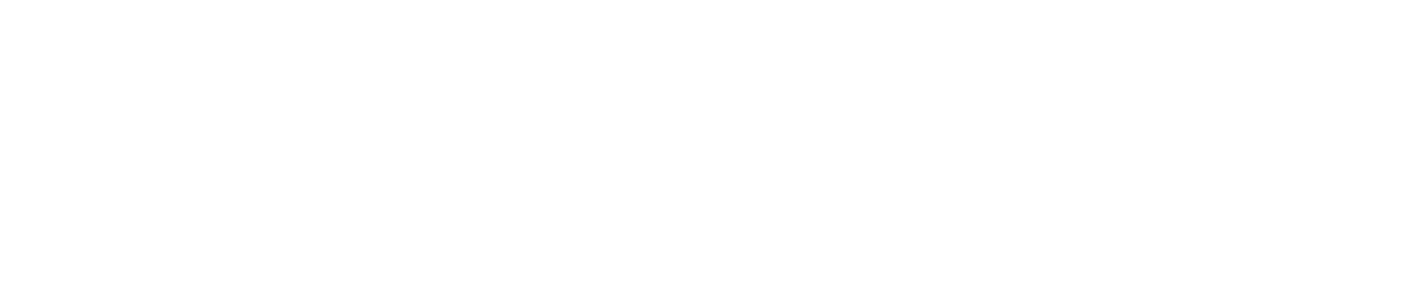